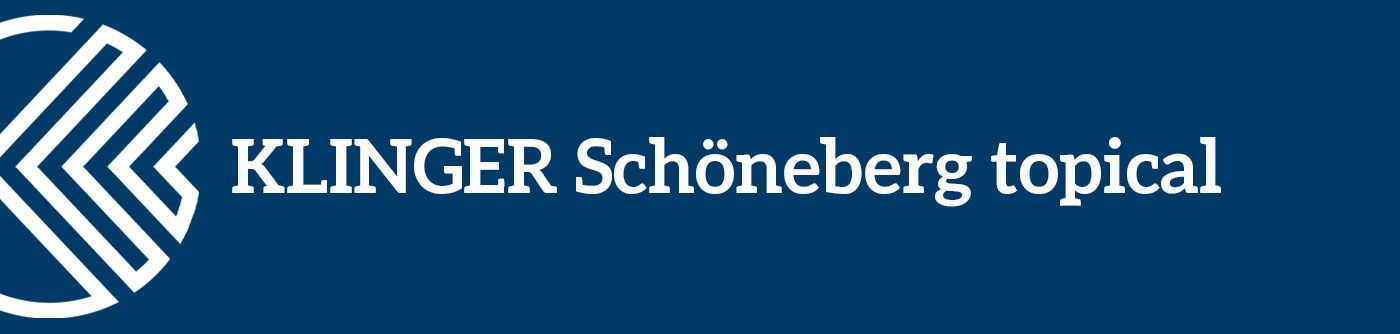
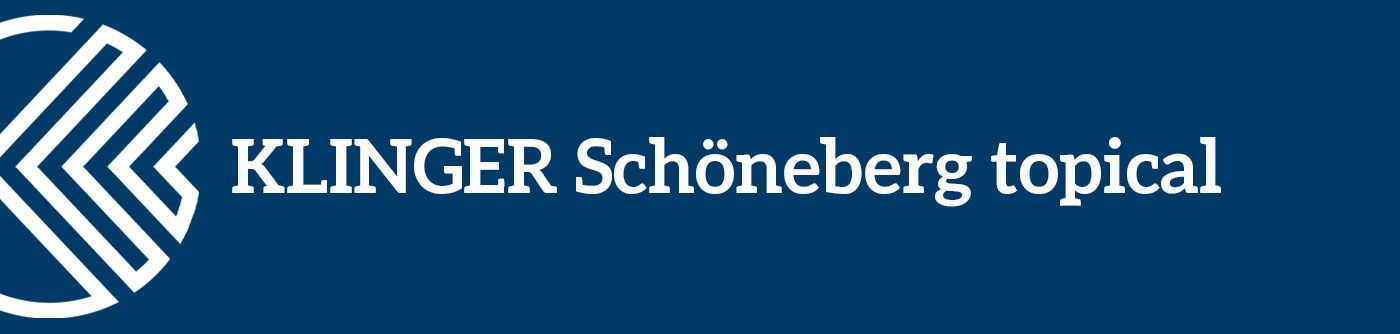
Supply of liquid-lubricated mechanical seals
Application in a petrochemical recycling plant.
Mechanical seals are considered the most reliable way of sealing pumps. To ensure the function of mechanical seals, the seal chamber between the product side and the atmospheric side is completely filled with a medium. For this purpose, a supply or barrier system is used in which the pressure of the sealing medium is higher than the process pressure to be sealed. In addition, the sealing system has the task of cooling the seal, building up the pressure in the seal chamber and ensuring circulation and cooling of the sealing liquid.
For shutting off and diverting the barrier medium (fully synthetic functional oil) into a cooling circuit, at 160°C and an operating pressure of 25 bar, KLINGER Schöneberg ball valves type INTEC K221-S-HT/11S NPS ¾" Class 300 with socket weld ends are used in the barrier system. This type is a floating and single side spring loaded metal-seated ball valve. The ball and ball-seats are made of Superduplex material (1.4980) and coated with a hard metal alloy of chromium carbide nickel/chromium by high velocity flame spraying.
The ball valves also have the task, in the event of mechanical seal leakage, to shut off the barrier system from the product being conveyed in order to ensure safety. This is a liquid plastic at 400°C which hardens immediately when cooled.
To protect the automation unit (consisting of a single-acting pneumatic actuator, the Vestamid limit switch box and the Norgren solenoid valve) from excessive temperature, mounting bracket and two stem extensions with a total height of 323 mm were built in combination.
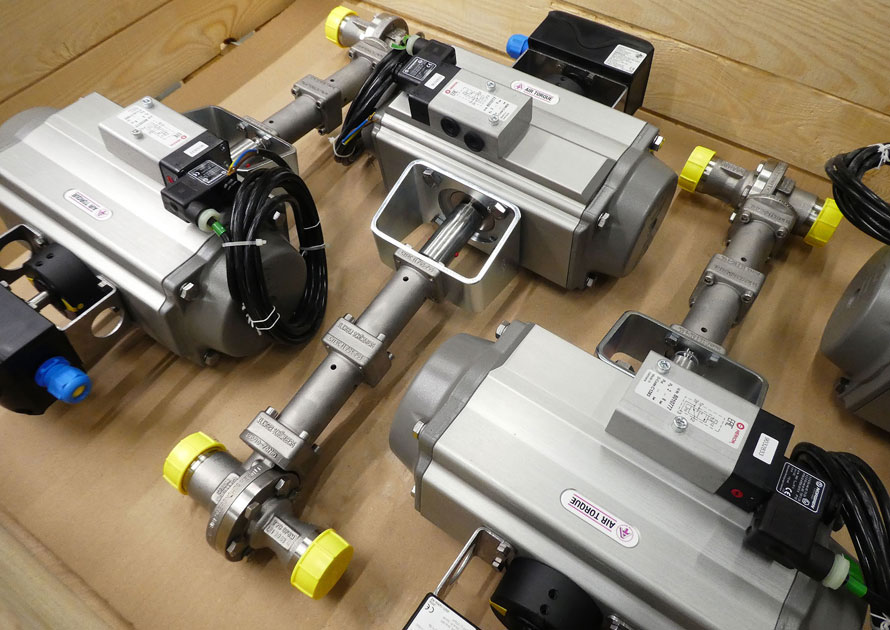
Ball valve type INTEC K221-S-HT/11S NPS ¾“ Class 300 with socket weld ends, mounting bracket and two stem extensions to protect the automation unit from excessive temperature
Your contact
- Marcel Gossmann, Business Development Manager / Management Assistent
+49 6126 950 - 268 marcel.gossmann@klinger-schoeneberg.de